1. Understanding Modern Pressure Washing Technology
Modern pressure washing technology has evolved significantly, combining advanced equipment specifications with precision-based applications. Today’s systems offer variable pressure settings, temperature control, and specialized attachments that make them highly versatile for different maintenance scenarios. Understanding these technological aspects is crucial for achieving optimal cleaning results while protecting surfaces.
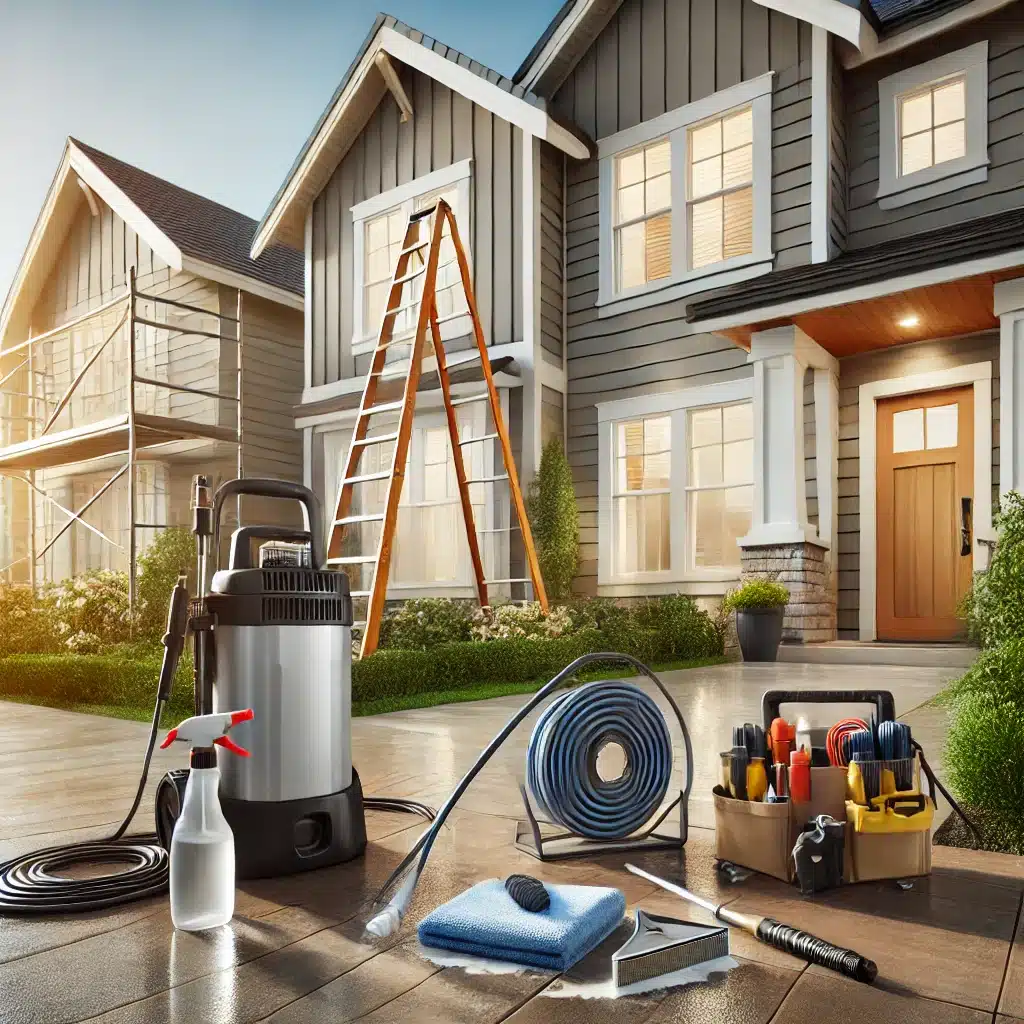
1.1 Evolution of Pressure Washing Equipment
The development of pressure washing equipment has moved from simple high-pressure water jets to sophisticated machines with digital controls and smart features. Modern units incorporate variable frequency drives (VFDs) that allow for precise pressure adjustment, reducing energy consumption and minimizing surface damage. Early systems operated at fixed pressures around 2,000 PSI, while current models offer ranges from 750 to 4,000 PSI with automatic pressure sensing.
Advanced pressure washers now feature integrated chemical injection systems, temperature monitoring, and remote operation capabilities. These improvements have led to a 40% reduction in water consumption compared to older models while achieving superior cleaning results. Key innovations include ceramic nozzle technology, quick-connect fitting systems, and thermal protection mechanisms.
1.2 Key Components and Specifications
Primary pressure washer specifications include:
Component | Function | Typical Range |
---|---|---|
Pump | Water pressurization | 2-5 GPM |
Motor | Power generation | 1.5-5.5 HP |
Nozzle | Spray pattern control | 0°-40° angles |
Hose | Water delivery | 25-100 ft length |
Essential features for professional equipment include thermal relief valves, unloader valves for pressure regulation, and downstream chemical injection systems. Modern units also incorporate digital pressure gauges, hour meters, and maintenance reminder systems that help optimize performance and extend equipment life.
1.3 Choosing the Right Pressure Level for Different Surfaces
Surface-specific pressure recommendations:
- Soft surfaces (wood, vinyl): 500-1,500 PSI
- Medium surfaces (concrete, brick): 2,000-3,000 PSI
- Hard surfaces (industrial equipment): 3,000-4,000 PSI
Proper pressure selection depends on surface condition, contamination level, and environmental factors. Assessment protocols should include surface hardness testing and small area trials before full-scale cleaning operations commence. Temperature selection is equally important, with hot water systems providing superior results for oil and grease removal.
2. Essential Site Equipment for Professional Maintenance
Professional maintenance operations require a comprehensive array of equipment beyond pressure washers. This includes support equipment for safety, transportation, and operational efficiency. Proper selection and integration of these components ensure smooth operations and optimal results.
2.1 Core Equipment Components and Their Functions
Essential maintenance equipment inventory includes:
- Primary cleaning units (pressure washers, surface cleaners)
- Water reclamation systems
- Chemical application devices
- Surface preparation tools
Support equipment requirements vary by project scale but typically include water tanks, generators, and portable containment systems. For professional-grade maintenance equipment and supplies, many contractors rely on specialized providers like National Site Supplies to ensure consistent quality and reliability. Modern maintenance operations also incorporate digital monitoring tools and automated chemical dispensing systems that ensure consistent application rates and reduce waste.
2.2 Safety and Personal Protective Equipment
Required safety equipment for pressure washing operations:
Equipment Type | Purpose | Replacement Frequency |
---|---|---|
Eye Protection | Impact/splash prevention | 6-12 months |
Foot Protection | Water/chemical resistance | 12 months |
Hand Protection | Chemical/pressure protection | 1-3 months |
Hearing Protection | Noise reduction | 3-6 months |
Safety protocols must address high-pressure injection risks, slip hazards, and chemical exposure. Regular safety training and equipment inspections are essential components of professional maintenance operations. Documentation systems should track equipment usage and maintenance histories.
2.3 Storage and Transportation Solutions
Equipment storage and transportation considerations focus on protection from environmental factors and efficient deployment. Climate-controlled storage areas prevent freeze damage to pumps and chemical degradation. Mobile storage solutions include:
- Weather-resistant equipment enclosures
- Chemical storage compartments
- Tool organization systems
- Quick-access safety equipment stations
Transportation systems must accommodate weight distribution requirements and provide easy access to frequently used items. Integrated loading ramps and secure tie-down points ensure safe equipment transport between job sites.
3. Integrating Pressure Washing with Site Maintenance
Integration of pressure washing into broader site maintenance programs requires careful planning and coordination. Successful integration maximizes resource efficiency while minimizing facility disruption. Key considerations include scheduling, equipment coordination, and performance monitoring.
3.1 Creating Effective Maintenance Schedules
Maintenance schedule optimization factors:
- Peak usage periods
- Weather conditions
- Resource availability
- Surface wear patterns
Regular maintenance intervals should be established based on surface type and exposure conditions. High-traffic areas typically require monthly attention, while peripheral areas may need quarterly service. Schedule coordination must account for drying times and surface preparation requirements.
3.2 Best Practices for Equipment Synergy
Equipment synergy maximization requires:
- Workflow optimization
- Resource sharing
- Cross-training personnel
- Standardized procedures
Effective integration involves coordinating pressure washing operations with other maintenance activities to minimize facility downtime. Equipment sharing protocols ensure maximum utilization while maintaining proper maintenance intervals and documentation.
3.3 Maximizing Operational Efficiency
Operational efficiency metrics include:
- Equipment utilization rates
- Resource consumption
- Labor productivity
- Quality outcomes
Performance monitoring systems track key metrics through digital logging and analysis tools. Regular efficiency assessments identify improvement opportunities and validate process modifications. Staff training programs focus on multi-skill development and operational flexibility.
4. Environmental Considerations and Sustainability
Environmental responsibility in pressure washing operations extends beyond water conservation to include chemical management and waste handling. Modern approaches emphasize sustainable practices while maintaining cleaning effectiveness. Key focus areas include water recycling, eco-friendly chemicals, and waste reduction.
4.1 Water Conservation Techniques
Water conservation strategies include:
- Closed-loop recycling systems
- Flow rate optimization
- Capture and reuse protocols
- Low-flow nozzle technology
Implementation of water conservation measures can reduce consumption by 50-80% compared to traditional methods. Advanced filtration systems enable water recycling while maintaining cleaning effectiveness through proper maintenance and monitoring.
4.2 Eco-friendly Cleaning Solutions
Environmental impact reduction through chemical selection:
Chemical Type | Benefits | Applications |
---|---|---|
Biodegradable | Quick breakdown | General cleaning |
pH Neutral | Surface safe | Sensitive materials |
Enzymatic | Organic matter | Food service areas |
Plant-based | Low toxicity | Public spaces |
Chemical management systems track usage and ensure proper dilution rates. Regular environmental impact assessments guide chemical selection and application protocols.
4.3 Waste Water Management Protocols
Proper wastewater management requires:
- Containment systems
- Filtration equipment
- Treatment protocols
- Disposal procedures
Collection and treatment systems must comply with local regulations while maintaining operational efficiency. Modern filtration technologies enable on-site water treatment and reuse, reducing disposal costs and environmental impact.
5. Cost-Benefit Analysis and ROI
Understanding the financial implications of pressure washing equipment and site maintenance integration is crucial for operational planning. Comprehensive analysis considers both direct costs and long-term benefits. Key factors include equipment investment, operational costs, and maintenance savings.
5.1 Initial Investment vs. Long-term Benefits
Investment considerations include:
Category | Initial Cost | Long-term Benefit |
---|---|---|
Equipment | High | Reduced replacement |
Training | Moderate | Improved efficiency |
Systems | Variable | Better outcomes |
Integration | Moderate | Lower operating costs |
ROI calculations must consider both tangible and intangible benefits, including extended asset life and improved appearance. Typical payback periods range from 12-24 months for comprehensive systems.
5.2 Maintenance Cost Reduction Strategies
Cost reduction approaches focus on:
- Preventive maintenance programs
- Resource optimization
- Training effectiveness
- Equipment longevity
Implementation of systematic maintenance programs typically reduces long-term costs by 25-40%. Regular equipment maintenance and operator training contribute significantly to cost reduction through improved efficiency and reduced downtime.
5.3 Performance Metrics and Quality Assessment
Key performance indicators include:
- Cleaning effectiveness
- Resource efficiency
- Cost per square foot
- Customer satisfaction
Quality assessment protocols incorporate regular inspections and documentation. Performance tracking systems enable continuous improvement through data analysis and process refinement.
6. Future Trends and Innovations
The pressure washing and site maintenance industry continues to evolve through technological advancement and operational innovation. Understanding emerging trends helps organizations prepare for future developments and maintain competitive advantages.
6.1 Emerging Technologies in Pressure Washing
Recent technological developments include:
- Robotics integration
- AI-powered cleaning systems
- Advanced surface recognition
- Automated pressure control
These innovations promise increased efficiency and improved outcomes through automated operation and precise control. Development focuses on reducing operator requirements while maintaining or improving cleaning effectiveness.
6.2 Smart Equipment Integration
Smart technology integration features:
- IoT connectivity
- Real-time monitoring
- Predictive maintenance
- Remote operation
Connected systems enable improved resource management and operational control. Data collection and analysis capabilities support continuous improvement and process optimization.
6.3 Predictive Maintenance Solutions
Predictive maintenance systems incorporate:
- Sensor networks
- Usage tracking
- Performance monitoring
- Maintenance scheduling
Advanced analytics enable proactive maintenance planning and reduced downtime. Integration with facility management systems supports comprehensive maintenance programs and resource optimization.